In contrast to porthole containers, integral refrigerated containers are equipped with their own refrigeration unit. This normally relies on a three-phase electrical power supply. For information on the electrical data of this container type, see Section 8.1.
Cold air flows through and around the goods in the container. This air is blown in through the gratings in the floor and then drawn off again below the container ceiling. The circulating fans then force the air through the air cooler, which also acts as the evaporator in the cold circuit, and back through the gratings into the cargo (see Figure 11).
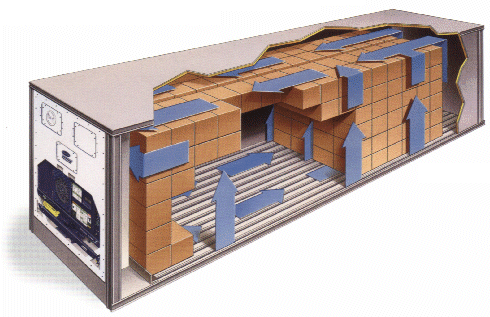
Figure 11: Air flow in an integral refrigerated container
Read More
In the case of precooled frozen goods, air only has to flow around the goods, since no heat has to be dissipated from the goods themselves. Only the heat which penetrates the insulation from outside has to be dissipated.
When transporting fruit, however, air flows through the goods, as fruit and vegetables generate respiration heat internally which has to be dissipated.
To ensure that air can flow around frozen goods, without however interrupting the normal flow of circulation while transporting fruit, the inner walls of the container normally feature corrugations. Then, even if the goods are stacked directly up against the wall, air will still flow through these channels and heat penetrating from outside will be dissipated.
Air exchange rates today are approximately 30 - 40 changes/hour when transporting frozen goods and approximately 60 - 80 changes/hour when transporting fruit. The pressure differential at the circulating fan (difference in pressure between the pressure side and the suction side) for normal stowage is approximately 12 - 25 mm H2O, but other values are possible, depending on the stowage, the power supply frequency and the extent to which the fresh air flaps are opened. Some newer container models have variable speed fans, where the speed is determined by the temperature differential between the supply air and the return air.
The goods must be stowed in the container in such a way that the air flow is not interrupted, for instance by stowing the goods too far above the red load limit line, and to avoid circulation bypasses, for instance as a result of free space in front of the door (where necessary, suitable measures must be taken to cover the grating here).
The container should only be precooled before loading if the container is loaded at an airlock, for instance in a cold store, so that the temperature outside the opened doors is approximately the same as the temperature inside the container. Otherwise, when the doors of a precooled container are opened, water will condense on the walls which may cause subsequent damage to the cargo.
Cold air flows through and around the goods in the container. This air is blown in through the gratings in the floor and then drawn off again below the container ceiling. The circulating fans then force the air through the air cooler, which also acts as the evaporator in the cold circuit, and back through the gratings into the cargo (see Figure 11).
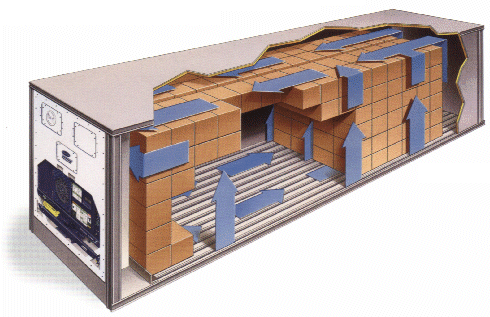
Figure 11: Air flow in an integral refrigerated container
Read More
In the case of precooled frozen goods, air only has to flow around the goods, since no heat has to be dissipated from the goods themselves. Only the heat which penetrates the insulation from outside has to be dissipated.
When transporting fruit, however, air flows through the goods, as fruit and vegetables generate respiration heat internally which has to be dissipated.
To ensure that air can flow around frozen goods, without however interrupting the normal flow of circulation while transporting fruit, the inner walls of the container normally feature corrugations. Then, even if the goods are stacked directly up against the wall, air will still flow through these channels and heat penetrating from outside will be dissipated.
Air exchange rates today are approximately 30 - 40 changes/hour when transporting frozen goods and approximately 60 - 80 changes/hour when transporting fruit. The pressure differential at the circulating fan (difference in pressure between the pressure side and the suction side) for normal stowage is approximately 12 - 25 mm H2O, but other values are possible, depending on the stowage, the power supply frequency and the extent to which the fresh air flaps are opened. Some newer container models have variable speed fans, where the speed is determined by the temperature differential between the supply air and the return air.
The goods must be stowed in the container in such a way that the air flow is not interrupted, for instance by stowing the goods too far above the red load limit line, and to avoid circulation bypasses, for instance as a result of free space in front of the door (where necessary, suitable measures must be taken to cover the grating here).
The container should only be precooled before loading if the container is loaded at an airlock, for instance in a cold store, so that the temperature outside the opened doors is approximately the same as the temperature inside the container. Otherwise, when the doors of a precooled container are opened, water will condense on the walls which may cause subsequent damage to the cargo.